I’ve had my Arca-Swiss 4×5 view camera for several years now, and more recently bought an 8×10 camera from my friend / mentor / boss Brenton Hamilton. It didn’t come with any lens boards, though, and rather than buying them off eBay or having somebody else make them, I decided to use my new skills (and a new friend) at TechShop to fabricate my own. Figured I’d make some additional boards for the 4×5 while I was at it.
The lens boards for the 8×10 camera – an Eastman Commercial View – are relatively straightforward – just 6in x 6in squares, nice and ‘merican and all. The Arca-Swiss lens boards are 171mm on a side, with 10mm radius rounded corners. Fortunately both are plain flat pieces of metal, without any complicated flanges or anything. I figured some time in Adobe Illustrator making the cut files, then a few minutes on the waterjet at TechShop, and I’d be done. Ha.
The waterjet, for those that don’t know, is this awesome room-sized machine that spits a mixture of water and grit out of a tiny nozzle at something like 60 gazillion psi – enough to cut through stainless steel plate – or 8 inches of stone – like it’s warm butter.
It’s pretty amazing, but I haven’t gotten around to taking the orientation and safety training that is required before I can use it, so I had to rope in somebody else to run my file for me. Dave, one of the guys that always seems to be having fun at TechShop, happened to be standing at the desk when I asked about this, and offered to do the cutting for me. Poor guy didn’t know what he was getting into!
Turns out I had a few issues. First, it wasn’t as simple as sending an Illustrator file to the waterjet like I would with the laser cutters. My vector file had to be translated into a set of paths (instructions) for the waterjet, and for some reason when I would bring the file into the waterjet software it took my nice lens board designs and made them look like Picasso had a go at them. Took a while to figure that out.
The waterjet – alone among all the TechShop toys tools – costs money for members to use: $2.00 per minute. (Everything else is part of the membership – just bring your own materials and blast / cut / weld / grind / sand away.) In what I thought was a cost-saving move, I had the metal supplier cut my 8×10 camera’s squares to the 6×6 inches, so all that was left was using the waterjet to cut nice neat Copal 1 and Copal 0 holes in the middle for the lenses.
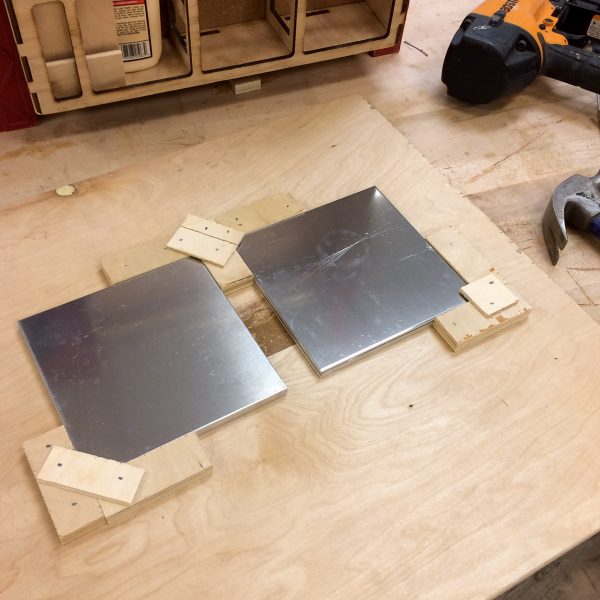
Well… putting pieces of metal that small in the waterjet might be problematic, so I had to build a rig to hold the boards for cutting. Just to be safe I mounted the larger sheet for the 4×5 boards on a big piece of scrap wood, too. On the plus side, I could easily stack all three of each size and cut them all at once: nearly a half inch of aluminum was nothing for the waterjet. (Update after taking the training: layers are also problematic, and maybe I should not have stacked them after all.)
When I showed up at TechShop to cut these boards I thought since I had prepared the Illustrator files and had the material already cut to size that it would only take 30 minutes or so. Finally, about four hours or so of work over two days, I had the cut lens boards in my hands. I spent another hour or so filing and sanding off sharp edges, and they were beautiful.
Next I wanted to paint them black on one side – may make them more colorful on the outside – and use the laser to etch my name, website, and the Copal hole size on the board.
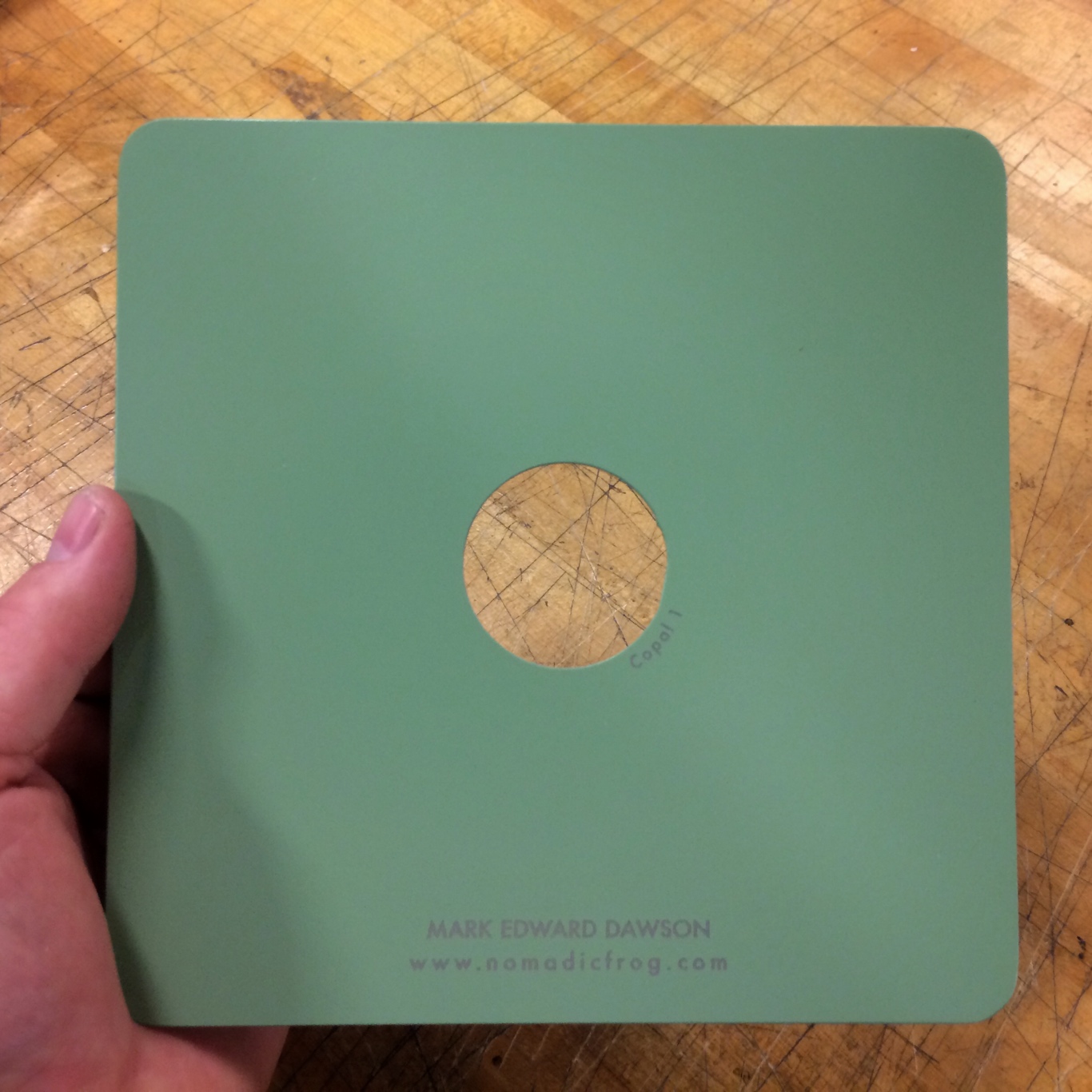

Side notes:
a) If anyone comes here by searching for Eastman Commercial View camera gear or something and has or knows of an extension rail / bed for sale, please let me know!
b) I’m signed up for the waterjet training in a few days, so I won’t have to torture poor Dave for my next waterjet job!
c) Speaking of “my next waterjet job”, I’m now taking orders for lens boards. :-)
Work an engineer would love.
Pingback: The Nomadic Frog Blog » Archive » Mark Dawson’s Best Campfire Beer Stake and Tequila Assistant